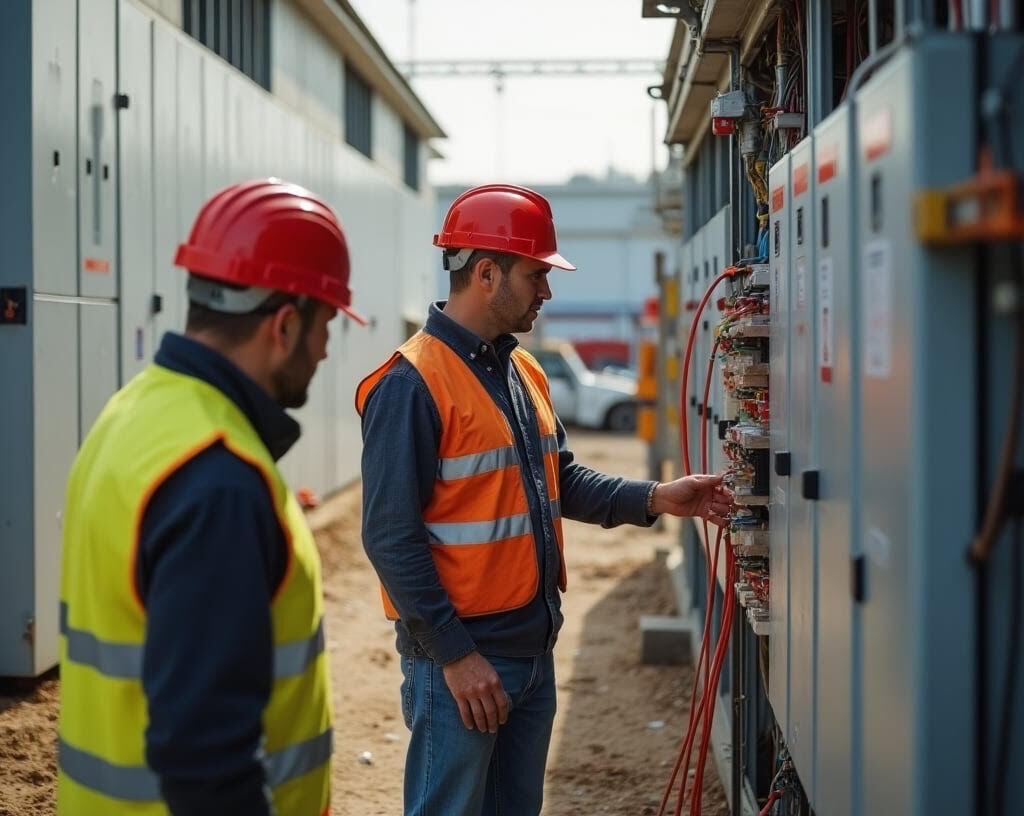
Electrical fires are a real threat on construction sites. Loose cables, temporary supplies, damaged equipment and wet weather all add up quickly if no one is paying attention.
It is not just the electricians’ job to think about fire safety. It is everyone's responsibility.
Construction sites are busy, messy environments. It only takes one fault, one overloaded socket or one missed check for a small spark to become a serious fire.
Site managers play a crucial role in ensuring that does not happen. They set the standards, plan for risks, and make sure the team has the right training and habits.
This article looks at practical ways to reduce the risk of electrical fires and keep construction sites safer for everyone.
Understanding the Main Causes of Electrical Fires on Site
Most electrical fires do not happen because of freak accidents. They happen because of simple, avoidable mistakes.
Damaged cables are a major problem. Tools dragged over rough ground, forklifts running over wires and heavy doors trapping leads all weaken insulation and expose live parts.
Overloaded circuits also pose significant risks. Temporary supplies are often not designed for heavy or long-term use. Plugging too many tools into one board can cause wiring to overheat rapidly.
Poor installation and rushed modifications cause further hazards. Quick fixes might seem harmless at the time, but they can easily overheat or short out later.
Neglecting regular checks allows these risks to build up unnoticed. Environmental factors such as wet weather, dust, and heavy machinery vibrations only make matters worse.
Understanding these causes is the first step towards preventing electrical fires on site.
The Importance of Electrical Safety Awareness for All Site Staff
Electrical safety is not just the domain of qualified electricians. Every worker, from labourers to supervisors, must have basic awareness.
They are the ones using tools, handling cables and moving equipment all day. They are also the ones likely to spot problems first — if they know what to look for.
Simple habits make a real difference. Recognising a damaged cable, avoiding running leads through doorways and reporting tripped breakers immediately are all actions that reduce risk.
Completing an electrical safety course gives workers an understanding of what safe practice looks like and helps them take precautions in unsafe scenarios. Short, focused sessions are often enough to build the right habits. They turn safety from a rule into an everyday behaviour.
When everyone on site is looking out for electrical risks, the chances of fire fall significantly.
Planning Safe Temporary Electrical Installations
Temporary electrical systems are a normal part of construction sites. However, temporary does not mean low quality.
Installations must be properly planned from the outset, designed for the specific site, set up by qualified electricians, and protected from weather, damage and interference.
Using robust distribution boards, protected cabling and proper earthing arrangements is essential. Fitting enough sockets is equally important to avoid daisy-chaining extension leads.
As the site evolves, installations must be adapted. Buildings going up, changing site layouts and increasing power demands all affect safe cable routes and equipment needs.
Good temporary installations make work easier and much safer. Temporary must never mean rushed or second best.
Daily Checks and Simple Measures to Reduce Fire Risk
Daily habits prevent serious incidents.
Before work starts, someone should check cables, sockets and boards for signs of damage, listen for buzzing and smell for burning. At the end of the day, workers should ensure everything is powered down properly, that no tools are left plugged in and that battery packs are stored safely.
Overloading sockets must be avoided. Boards should be properly rated for site load. Tools should never be hung by their leads or cables dragged across busy walkways.
Workers must be encouraged to report faults immediately and not resort to temporary fixes or 'making do' for another day.
Small, regular checks keep risks low and help prevent fires from starting.
How Training and Site Culture Can Prevent Complacency
Rules written on paper do not stop fires. People do.
Training teaches staff what to look for, but culture is what keeps them alert every day, even when workloads are heavy.
A strong safety culture ensures workers know they are expected to report faults without fear of blame. It builds trust that managers will act quickly to fix problems.
Bad habits spread easily if left unchallenged. Fortunately, good habits spread too.
Running refresher sessions, site safety stand-downs and regular toolbox talks helps keep electrical risks front of mind.
Training should link into wider site expectations. Completing proper construction compliance training ensures that workers and managers understand their duties around safe systems of work, electrical risks and reporting procedures.
A safety-first culture is built steadily, one action at a time.
Best Practices for Managing Electrical Equipment and Tools
Managing tools and equipment properly is not only about saving money. It is about saving lives.
Sites should set up clear inspection routines, including daily visual checks by users, weekly checks by supervisors and formal Portable Appliance Testing (PAT) where needed.
Faulty tools must be tagged and removed from use immediately. Allowing damaged equipment to stay in circulation, even for "just one more use", creates serious risks.
All electrical points should be clearly labelled, showing where the power comes from and what it supplies.
Use construction-grade tools, not domestic-grade equipment that cannot withstand site conditions.
Proper storage is also essential. Throwing cables onto muddy ground or shoving tools into vans damages insulation and connectors. Dry, secure storage prevents many problems before they start.
Good equipment management keeps sites safer without slowing down work.
Emergency Planning: Preparing for Electrical Fire Risks
Even with the best systems, accidents can happen.
Every construction site must have a clear emergency plan that covers electrical fire risks. This includes early installation of fire detection systems such as temporary alarms and emergency lighting, and maintaining safe exit routes even in partially built areas.
Fire extinguishers must be appropriate for electrical fires. CO₂ or dry powder extinguishers should be used, never water-based ones.
Workers must be trained to raise alarms correctly and know when and how to use extinguishers safely. Equally, they must know when not to attempt tackling a fire and to evacuate instead.
Emergency plans must be reviewed and updated regularly as the site changes. A plan that worked during groundworks may not be suitable when structures are partially enclosed.
Preparation saves lives when seconds matter.
Electrical fires on construction sites rarely happen without warning. They grow from small mistakes, bad habits and ignored warnings.
Preventing them is not complicated. It takes planning, proper training, daily checks and quick action when problems appear.
Construction site managers lead the way. By setting high standards and sticking to them, they create sites where everyone can work safely.
Electrical safety is not about luck. It is about taking consistent, deliberate action every single day.
(0) comments
We welcome your comments
Log In
Post a comment as Guest
Keep it Clean. Please avoid obscene, vulgar, lewd, racist or sexually-oriented language.
PLEASE TURN OFF YOUR CAPS LOCK.
Don't Threaten. Threats of harming another person will not be tolerated.
Be Truthful. Don't knowingly lie about anyone or anything.
Be Nice. No racism, sexism or any sort of -ism that is degrading to another person.
Be Proactive. Use the 'Report' link on each comment to let us know of abusive posts.
Share with Us. We'd love to hear eyewitness accounts, the history behind an article.