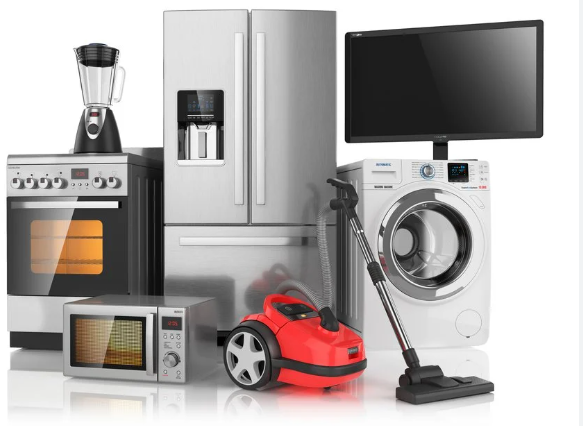
The right materials are crucial for producing high-quality products in today's competitive market. Companies aim to deliver durable goods that properly meet customer expectations. Choosing superior materials ensures that the final product upholds these standards, builds customer loyalty, and strengthens the brand's reputation.
Exploring the Characteristics of Materials
A fundamental step in creating a high-quality blank is selecting the appropriate materials for its construction. Whether dealing with fabrics, metals, or plastics, the material properties considerably affect the blank's durability. Understanding these properties helps in making informed choices. For instance, many prefer cotton for its breathability and comfort, which makes it ideal for apparel blanks. When selecting a sublimation blank, it's essential to consider how well the material absorbs dyes and maintains color vibrancy. Analyzing the intended use of the blank guides the material selection process and ensures the final product performs as expected.
Analyzing Methods Used in Production Environments
The techniques employed during manufacturing greatly influence the quality of the materials used. Advanced production methods achieve precision and durability. It’s essential to evaluate potential suppliers based on their ability to maintain strict quality control measures. Suppliers integrating automation and the latest technological advancements into their processes tend to produce more reliable materials. This factor reduces the likelihood of errors commonly associated with manual labor and consistently delivers high-quality blanks.
Evaluating the Credibility of Suppliers
The supplier's reputation plays a pivotal role in the quality of materials used in production. Establishing a strong relationship with reputable suppliers ensures a steady supply of top-tier materials. Researching supplier backgrounds, reading reviews, and consulting industry peers can provide valuable insights into their reliability. Trustworthy suppliers are committed to quality, demonstrate honesty, and offer excellent customer support, all critical factors in maintaining product excellence.
Ensuring Continuity
Maintaining consistency in the blanks used is essential for customer satisfaction. Variations in blanks can lead to product design and functionality discrepancies while undermining customer trust. Establishing clear guidelines and maintaining open communication with suppliers is essential for uniformity. Requesting samples before placing large orders allows you to verify consistency and quality firsthand, thus ensuring that each batch meets your standards.
Focusing on Longevity
The durability and lifespan of a product are key factors in customer satisfaction. Products that endure over time receive positive feedback and encourage repeat business. When selecting materials for a sublimation blank, choose those known for their strength and resilience. Conducting durability tests, such as stress and wear assessments, helps ensure that the blanks can withstand prolonged use without compromising quality.
Factors Related to Sustainability
Sustainability has become increasingly important to consumers, who prefer environmentally friendly products. Selecting materials and production processes that minimize environmental impact can enhance your brand’s image and attract eco-conscious customers. Partnering with suppliers prioritizing sustainable practices aligns with broader business objectives and appeals to a growing market segment that values responsible production.
Ensuring Quality Standards
Implementing comprehensive testing and quality assurance procedures is vital to meet the expected product standards. A robust testing system helps identify weaknesses before the product reaches the consumer. Quality checks should include verifying dimensional accuracy, material composition, and performance under various conditions. Collaborating closely with suppliers to develop practical testing protocols can prevent defects and maintain high-quality standards consistently.
Regarding Customer Input and Adjustments
Listening to customer feedback provides valuable insights into your products' market performance. Understanding customers' experiences with the durability and satisfaction of your products highlights areas for improvement. Adapting your product offerings based on this feedback can enhance customer satisfaction and loyalty. Maintaining open lines of communication with your customers builds trust and encourages ongoing engagement with your brand.
Selecting high-quality blanks requires a comprehensive approach that includes understanding material characteristics, assessing supplier credibility, and maintaining consistency and durability. Considering sustainability and adhering to strict quality standards further ensures customer satisfaction and loyalty. By prioritizing these factors, companies can deliver superior products that meet customer expectations and strengthen their market position.
(0) comments
Welcome to the discussion.
Log In
Keep it Clean. Please avoid obscene, vulgar, lewd, racist or sexually-oriented language.
PLEASE TURN OFF YOUR CAPS LOCK.
Don't Threaten. Threats of harming another person will not be tolerated.
Be Truthful. Don't knowingly lie about anyone or anything.
Be Nice. No racism, sexism or any sort of -ism that is degrading to another person.
Be Proactive. Use the 'Report' link on each comment to let us know of abusive posts.
Share with Us. We'd love to hear eyewitness accounts, the history behind an article.